Process
GRP profiles and their production method for Pultrusion
The pultrusion process is a continuous manufacturing method, as shown
outlines and is used in the production of uniform section product using
various resin types including polyester resin or epoxy estervinílica
phenolic, reinforced with glass fibers, superior performance to the materials
conventional and includes two stages in its manufacture.
Step 1: Impregnation of the fibers in a liquid resin into the heated mold,
the shape of the desired section.
Step 2: Cure / solidification of the matrix resin into the mold, forming the
desired geometry.
Characteristics of FRP
The STEP remains secure its strategy to develop, design and install
solutions PFRV profiles, incorporating in their supplies and works the
great advantages that these materials have relatively to steel and
more traditional constructive solutions and briefly
include:
- The GRP profiles are four times lighter than its equivalent steel and have a weight 30% less than aluminum.
- GRP have a high mechanical, electrical, thermal and corrosion resistance.
- Composite materials provide superior properties of each individual component because their properties are very high and can even exceed metals.
- By combining two or more different materials (components), we obtain specific mechanical properties such as strength and characteristics desired.
The most important conclusion to be drawn about the FRP is that these materials have specific properties
higher than the said conventional materials as figure and table below:
- Linear elastic until breaking (no ductility).
- Orthotropic behavior.
- High longitudinal resistance (similar to steel).
- Lower modulus of elasticity than steel.
- Low density (less than 4 times that of steel).
Property |
Direction parallel to the fibers (x) |
Cross Directorate to the fibers (y) |
Tensile strength (MPa) |
200-400 |
50-60 |
Compressive Strength (MPa) |
200-400 |
70-140 |
Shear strength (MPa) |
25-30 |
Modulus of elasticity (GPa) |
20-40 |
5-9 |
Shear Modulus (GPa) |
3-4 |
Content in fiber mass |
50-70 |
Density |
1.5-2.0 |
Coeficinete of thermal expansion |
8-14 |
16-22 |
Condutabilidade Thermal Coefficient (W / K.m) |
0.20-0.58 |
Technical specifications for all kinds of FRP profiles |
specific Resistance |
10^10-10^15 Ohm/cm |
Higher isolation as resistance |
10^10-10^15 Ohm |
Dielectric strength |
5-10 kV/mm |
Thermal extension coefficient |
12*10-6 1/K |
Thermal conductivity |
0,2 - 0,6 W/m*K |
Specific temperature Capacity |
1,0 - 1,2 kJ/kg*K |
Temperature resistance |
-100 - +155 (180)°C |
Water absorption |
0,15% |
Temperature Resistance (Marten) |
200°C |
Fire resistance |
B2, UL94 V1, UL94 V0, DIN 5510 S4 SR2 ST2, ASTM E84 < 25, ASTM D635 |
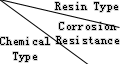 |
Type V |
Type I |
Type O |
Concentration
% |
Temperature
F/℃
|
Concentration
% |
Temperature
F/℃
|
Concentration
% |
Temperature
F/℃
|
Acetic Acid |
50 |
180/82 |
50 |
125/52 |
5 |
77/25 |
Aluminum
Hydroxide |
100 |
180/82 |
100 |
160/71 |
ALL |
- |
Ammonium
Chloride |
ALL |
210/99 |
ALL |
170/77 |
ALL |
- |
Ammonium
Bicarbonate |
50 |
160/70 |
15 |
125/52 |
ALL |
- |
Methacrylic
Acid |
99 |
95/35 |
- |
- |
- |
- |
Ammonium
Hydroxide |
28 |
100/38 |
28 |
N/R |
ALL |
N/R |
Ammonium
Sulfate |
ALL |
210/99 |
ALL |
170/77 |
ALL |
- |
Benzene |
100 |
92/40 |
ALL |
N/R |
ALL |
N/R |
Benzoic
Acid |
SAT |
210/99 |
SAT |
150/66 |
ALL |
77/25 |
Borax |
SAT |
210/99 |
SAT |
170/77 |
SAT |
113/45 |
Calcium
Carbide |
ALL |
180/82 |
ALL |
170/77 |
ALL |
- |
Calcium
Nitrate |
ALL |
210/99 |
ALL |
180/82 |
ALL |
- |
Carbon
Tetrachloride |
100 |
92/40 |
100 |
N/R |
100 |
N/R |
Cholrine,
Dry Gas |
- |
210/99 |
- |
140/60 |
- |
N/R |
Chlorine
Water |
SAT |
200/93 |
SAT |
80/27 |
SAT |
N/R |
Chromic
Acid |
10 |
150/65 |
5 |
70/21 |
5 |
N/R |
Citric Acid |
ALL |
210/99 |
ALL |
170/77 |
ALL |
77/25 |
Calcium
Chloride |
ALL |
210/99 |
ALL |
170/77 |
ALL |
104/40 |
Copper
Cyanide |
ALL |
210/99 |
ALL |
170/77 |
ALL |
77/25 |
Copper
Nitrate |
ALL |
210/99 |
ALL |
170/77 |
ALL |
- |
Ethanol |
10 |
155/82 |
50 |
75/24 |
10 |
77/25 |
Ethylene
Glycol |
100 |
200/93 |
100 |
90/32 |
100 |
104/40 |
Hydrofluoric
Acid |
10 |
149/65 |
- |
- |
- |
- |
Ferric
Chloride |
ALL |
210/99 |
ALL |
170/77 |
ALL |
104/40 |
Ferrous
Chloride |
ALL |
210/99 |
ALL |
170/77 |
ALL |
86/30 |
Formaldehyde |
37 |
140/60 |
50 |
75/24 |
25 |
86/30 |
Gasoline |
100 |
180/82 |
100 |
75/24 |
100 |
95/35 |
Glucose |
100 |
210/99 |
100 |
170/77 |
ALL |
- |
Glycerine |
100 |
210/99 |
100 |
150/66 |
100 |
- |
Hydrobromic
Acid |
50 |
150/65 |
50 |
120/49 |
18 |
- |
Hydrochloric
Acid |
37 |
150/65 |
37 |
75/24 |
10 |
86/30 |
Hyrogen
Peroxide |
30 |
150/65 |
5 |
100/38 |
5 |
N/R |
Lactic Acid |
ALL |
210/99 |
ALL |
170/77 |
ALL |
77/25 |
Lithium
Chloride |
SAT |
210/99 |
SAT |
150/66 |
ALL |
- |
Magnesium
Chloride |
ALL |
210/99 |
ALL |
170/77 |
ALL |
104/40 |
Magnesium
Nitrate |
ALL |
210/99 |
ALL |
140/60 |
ALL |
86/30 |
Magnesium
Sulfate |
ALL |
210/99 |
ALL |
170/77 |
ALL |
104/40 |
Mercureic
Chloride |
100 |
210/99 |
100 |
150/66 |
100 |
104/40 |
Mercurous
Chloride |
ALL |
210/99 |
ALL |
140/60 |
ALL |
104/40 |
Nickel
Chloride |
ALL |
210/99 |
ALL |
170/77 |
ALL |
104/40 |
Nickel
Sulfate |
ALL |
210/99 |
ALL |
170/77 |
ALL |
104/40 |
Nitric Acid |
20 |
130/54 |
20 |
70/21 |
20 |
N/R |
Oxalic Acid |
ALL |
210/99 |
ALL |
75/24 |
ALL |
N/R |
Perchloric
Acid |
30 |
100/38 |
10 |
N/R |
10 |
N/R |
Phosphoric
Acid |
100 |
210/99 |
100 |
120/49 |
80 |
N/R |
Potassium
Chloride |
ALL |
210/99 |
ALL |
170/77 |
ALL |
104/40 |
Potassium
Dichromate |
ALL |
210/99 |
ALL |
170/77 |
ALL |
77/25 |
Potassium
Nitrate |
ALL |
210/99 |
ALL |
170/77 |
ALL |
104/40 |
Potassium
Sulfate |
ALL |
210/99 |
ALL |
170/77 |
ALL |
104/40 |
Propylene
Glycol |
ALL |
210/99 |
ALL |
170/77 |
ALL |
104/40 |
Sodium
Acetate |
ALL |
210/99 |
ALL |
160/71 |
ALL |
104/40 |
Sodiumt
Bisulfate
|
ALL |
210/99 |
ALL |
170/77 |
ALL |
- |
Sodium
Bromide |
ALL |
210/99 |
ALL |
170/77 |
5 |
- |
Sodium
Cyanide |
ALL |
210/99 |
ALL |
170/77 |
5 |
N/R |
Sodium
Hydroxide |
25 |
180/82 |
N/R |
N/R |
N/R |
N/R |
Sodium
Nitrate |
ALL |
210/99 |
ALL |
170/77 |
ALL |
104/40 |
Sodium
Sulfate |
ALL |
210/99 |
ALL |
170/77 |
ALL |
104/40 |
Stannic
Chloride |
ALL |
210/99 |
ALL |
160/71 |
ALL |
104/40 |
Sulfuric
Acid |
50 |
183/80 |
25 |
75/24 |
10 |
- |
Tartaric
Acid |
ALL |
210/99 |
ALL |
170/77 |
ALL |
- |
Vinegar |
100 |
210/99 |
100 |
170/77 |
ALL |
- |
Methanol |
10 |
183/84 |
N/R |
N/R |
N/R |
N/R |
Sea Water |
ALL |
210/99 |
ALL |
158/70 |
ALL |
113/45 |
Water,
Distilled |
100 |
180/82 |
100 |
170/77 |
ALL |
86/30 |
Zine Nitrate |
ALL |
210/99 |
ALL |
170/77 |
ALL |
104/40 |
Zine Sulfate |
ALL |
210/99 |
ALL |
170/77 |
ALL |
104/40 |
The use of phenolic resins, available in our range of products from that previously requested, is the
resin suitable for all applications where fire resistance is mandatory. This resin to be
incorporated into the manufacture of profiles has as its main features the great resistance
flames and high temperature (900 ° C), not releasing fumes and having low emission of toxic gases,
It is the right solution for environments where fire safety is of great importance.
Compliance with the standards, ASTM E84, ASTM E119 Level 2 (L2), ASTM D2565, ASTM D 5630, ASTM D 2583,
NES 713 being the only resin approved by USCG-USA for use in level 2 (escape route)
according to ASTM E-84 and ASTM E-119.